Logging out of EU Login will log you out of any other services that use your EU Login account. Use the CORDIS log out button to remain logged in on other services.
Article available in the following languages: Cellulose Fiber
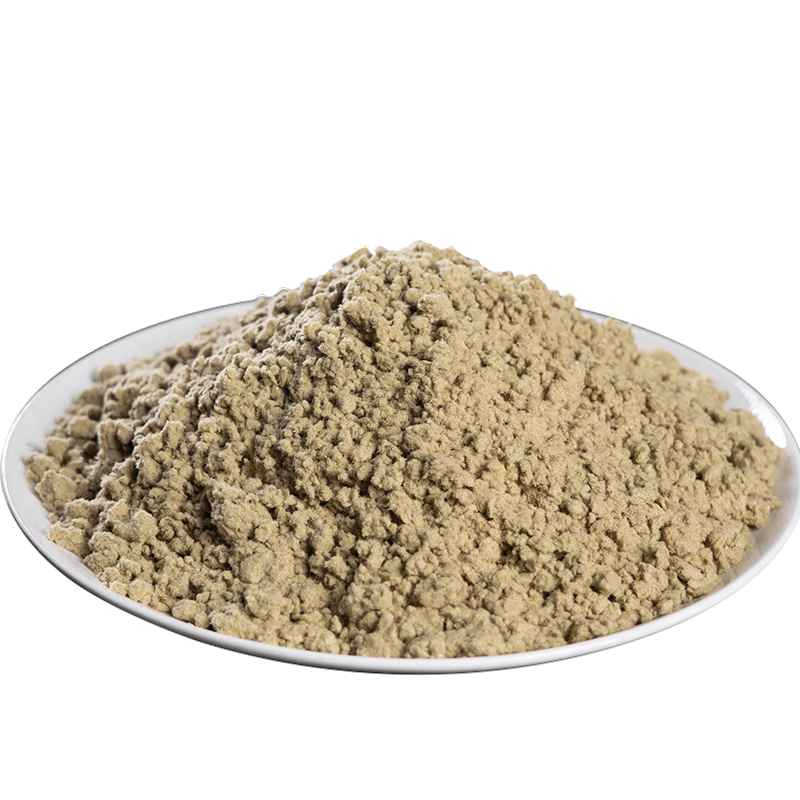
Mineral wool building insulation could soon be diverted from landfills and used to make geopolymer concrete and 3D-printed construction elements, slashing CO2 emissions.
Construction and demolition waste accounts for more than a third of all waste generated in the EU. Mineral wool, widely used with other insulation materials, has a very low density meaning disposing of it requires a disproportionate volume. Further, this fibrous spun mixture made from molten glass, rock or slag is considered largely unrecyclable. All that is changing thanks to the EU-funded WOOL2LOOP project, which has demonstrated the use of mineral wool as a precursor for making geopolymer concrete and associated construction elements on an industrial scale in a circular economy business model.
Geopolymers, also called alkali-activated materials, are ceramic-like inorganic polymers made from solid aluminosilicates cross-linked with alkali metal ions. “Geopolymer concrete made from volcanic ash (rich in aluminosilicates) can be found in the Colosseum, the Pantheon and the Egyptian pyramids,” explains project coordinator Anne Kaiser of Saint-Gobain Finland. Geopolymers are a promising binder for concrete production because their production requires far less energy than conventional Portland cement. WOOL2LOOP set out to convert mineral wool waste from construction demolition into mineral wool geopolymers and demonstrate new product production on an industrial scale meeting the specifications of commercially available products with a lower carbon footprint.
The project was complex, encompassing all phases of mineral wool use and the current challenges to recycling it. It required: smart demolition practices, mineral wool sorting and milling to produce mineral wool powder, alkali activation to produce geopolymers, geopolymer concrete production and 3D printing of construction elements using it. As Eldho Choorackal of CRH explains, all of this was further complicated by the fact that “there are no standards or guidelines for industrial-scale production and quality control of geopolymer concrete precast elements.” “WOOL2LOOP adopted and tested the use of a handheld X-ray fluorescence spectroscopy device for on-site analysis of mineral wool waste to distinguish between glass wool and stone wool,” explains Johan D’Hooghe of Recycling Assistance. The waste was then milled at a centralised location. “Producing the mineral wool powder was particularly challenging given the different chemical compositions of glass wool and mineral wool and the need to obtain materials with a particle size less than 100 micrometres,” adds Vilma Ducman of the Slovenian National Building and Civil Engineering Institute. “The milling and mix designs associated with mineral wool, a prerequisite for subsequent processing and scale-up, required significant innovation,” adds Saleh Hooshmand, Senior Research Associate at Saint-Gobain Ecophon. Additive manufacturing, or 3D printing, of construction materials and particularly geopolymers posed additional challenges. “Innovations in hardware, software and the chemical activation strategy enabled us to control the materials’ formation. We are now able to produce complex geometries for many products with new functionalities, including acoustic panels, on a large scale with 3D printing. The next goal is certification of these materials and processes,” explains Alban Mallet of XtreeE. WOOL2LOOP successfully demonstrated the production of precast mineral-wool geopolymer concrete on an industrial scale, accumulating essential knowledge about all processes and materials along the recycling and production chain. “By conducting pilot projects with so many mineral wool geopolymer-based products, we have been able to identify potential problems that can be expected in regular production. We will now focus on finding ways to overcome these,” concludes Ducman.
WOOL2LOOP, mineral wool, geopolymer concrete, construction, geopolymers, 3D printing, alkali activation, circular economy, additive manufacturing, X-ray fluorescence microscopy
Permalink: https://cordis.europa.eu/article/id/443256-mineral-wool-finds-new-life-in-a-familiar-environment
Your data extraction with Task ID TASK_ID_PLACEHOLDER is available for download.
Your booklet {{ title }} generated on {{ timestamp }} is available for download.

Fiber Glass Wool The file will remain available for {{ hours }} hours, or until you close your browser.