The global transition toward creating a greener and more environmentally friendly society requires transmission system operators (TSOs) to consider refining their existing installation methods, increasing their focus on worker safety and investigating the possibility of using new tower materials. To satisfy dual objectives is now a tough challenge many TSOs face.
The transmission system in Norway crosses remote areas, which has a considerable impact on line construction, especially in mountainous terrain and areas without access roads. Helicopters are used extensively to transport materials and in the erection of supporting towers. Reducing the time spent erecting and working on transmission line towers as well as minimizing the use of helicopters and the carbon footprint would result in a win-win solution. Any new tower type should offer the same service life and system reliability of today’s towers as well as be aesthetically acceptable. Fiberglass Reinforcing Rod
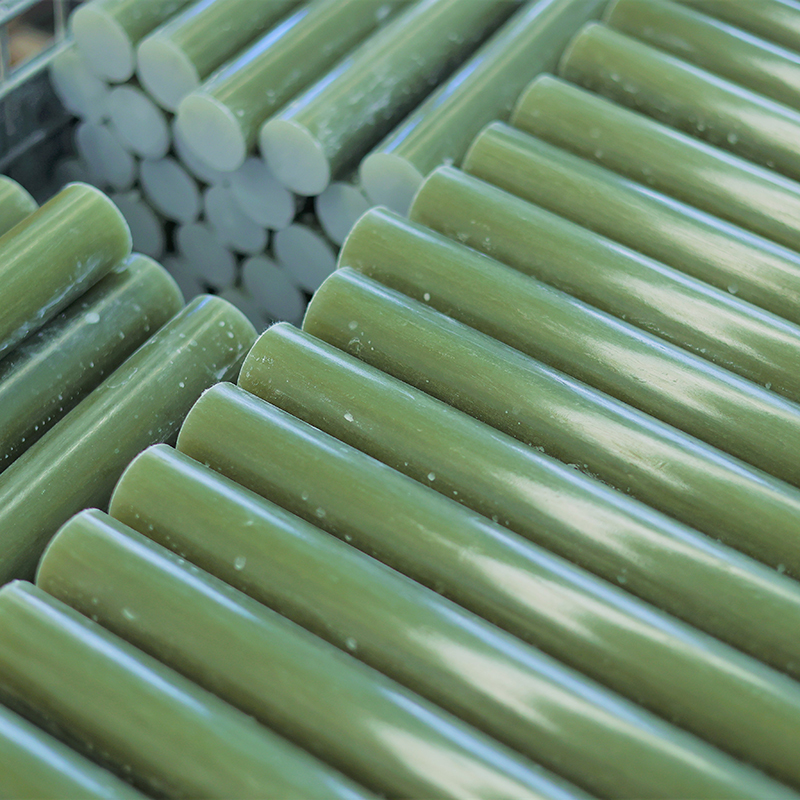
Statnett SF is collaborating with DNV and Engelbrecht Consulting BV to investigate the use of transmission line towers made of composite materials, namely fiberglass. Generally, the use of composite towers is limited to supporting circuits rated 132 kV and below. Statnett completed its first 132-kV transmission line section with composite poles in 2014. The collaborative research program is focused on a conceptual tower design that uses fiber-reinforced polymers (FRP) to support conductors on a 420-kV transmission system.
Composite materials have been used in transmission lines before, in both towers at 132 kV and insulators at 420 kV. However, using FRP on a complete tower for a 420-kV transmission line is completely different. While dry composite materials have an electrically insulating surface, it becomes partly conductive when wet. In effect, FRP towers are essentially nonconductive but they become (semi) conductive when wet, presenting challenges in terms of the electrical design.
This characteristic means the separation distances on the tower must be taken into consideration. The specified air gaps need to ensure all flashovers go over the insulator string or to designated points on the tower. Tower sections where field concentrations occur that potentially accelerate material degradation also must be avoided.
In addition, an independent earthing system needs to be included that provides an electrical path to earth for any of the fault currents that might arise on the transmission line during its service life. This earthing system must be designed in a way that prevents it from overheating, irrespective of the type of overhead line fault and subsequent fault current.
In Norway, all transmission lines must conform with the European standard, EN 50341-1, and national normative aspects for Norway, NEK EN 50341-2-16. At 400 kV, this standard assumes a fully conductive support structure. Thus, several additional requirements must be included to deal with the application of composite materials.
The following measures must be taken into consideration:
Despite these challenges, the use of composite towers exhibits great promise, as larger sections can be flown to a site and built by a ground-based workforce more quickly than constructing a sectional tower above ground level. This also means the use of a helicopter can be greatly reduced, increasing worker safety and lowering installation costs.
For this project, a design methodology had to be developed. The electrical design parameters for steel towers were altered to accommodate all aspects of the composite tower. This served as the design basis on which other elements were added.
The rest of the project was divided into several work packages, each constituting a separate milestone. The workflow was set up as an iterative process, meaning design changes and revisions could be consolidated into the design as it moved forward. Elements having the largest potential impact on the tower design (such as material selection and insulation coordination) were addressed first and locked before proceeding on to elements with a smaller impact. This meant as the project progressed, the design team could encircle the final design with all the detailing necessary. It also was vital to determine a workflow that could support an expected service life of 70 years.
During the early stages of planning a transmission line, not every key design parameter is known. For example, in Norway, pollution levels have been quite low historically but wind and ice loading on the conductors severe. Composite towers may not initially be suitable for all climatic conditions and loads, so it was essential to identify this tower type’s limitations.
The tower material was designed for ambient temperatures between –50°C and +60°C (–58°F and 140°F) as well as an average annual horizontal irradiation of approximately 950 kWh/sq m (88 kWh/sq ft). The completed tower was designed for wind loads up to 44 m/s (144 ft/s), ice loads up to 10 kg-m (6.72 lb-ft) and low pollution levels.
The composite materials and their formulas are subject to strict confidentiality. Therefore, it can be difficult for a purchaser to ensure proper quality, especially when seeking the most appropriate material available from several manufacturers. Similar composite samples can display vastly different characteristics and behavior when subject to the same tests. Statnett’s goal was to establish a test regime that would enable a purchaser to qualify or disqualify composite samples based on a standard set of test requirements. The tests also set out to try and provide an indication of any type of challenge that might arise from the different composite material test samples during service life.
A series of tests were first conducted on two composite material samples provided by each manufacturer. One striking and noticeable difference identified when subject to the dye penetration test (IEC 62217) was the difference in water ingress seen between each of the two samples. It was evident samples tested from one manufacturer were much more porous and, therefore, more susceptible to water ingress and subsequent internal freezing. The porousness would increase the mechanical stress applied to the composite material and reduce the expected service life.
From the early tests completed, Statnett was able to make some in-house system voltage-independent recommendations for linemen working on composite towers:
In addition, electrical field grading of components would be necessary to avoid the risk of tracking and erosion on higher-voltage transmission lines — just to specify that that the concern is on the surface of the material.
This project required the qualifying theoretical designs to be subjected to full-scale testing. Therefore, a test on a completed 1-to-1 composite model involving full-scale testing using tubes was conducted in Prague in 2018. The prototype developed for testing was built using aluminum tubes to simulate a wet structure. This ensured the tests would be based on conservative results. Although the conductors were static, all other components in the model could be moved individually, allowing the modeling and testing of all relevant electrical separation distances.
Lightning and switching impulse tests were performed on the full-scale prototype tower. The aim was to determine the minimum air clearances necessary to ensure no flashovers occurred directly to the composite section of the tower. To pass the test, the impulse-withstand voltages for both lightning and switching had to be equal to or higher than Statnett’s conventional steel towers.
For the impulses, an up-down sequence and subsequent impulses with respective correctional factors were used to determine the lightning and switching impulse-withstand voltages. While the lightning impulses used 20 impulses, the switching impulses used 40 impulses, as the flashover path during a switching surge is less predictable than lightning.
The prototype tower used glass cap-and-pin insulator strings, and it was found lightning impulse flashovers tended to hug either side of an insulator string. However, Statnett’s policy is to install mainly glass cap-and-pin insulator strings, as they are easily replaced and have a proven service record glass cap-and-pin insulator strings, as they have an low failure rate, and shattered insulators requiring replacement are easily detected. Hence, Statnett already had decided that when 420-kV composite towers were used in service, the overhead line conductors would be insulated by glass cap-and pin insulator strings.
During this series of tests, it also was noted the insulator flashovers tended to go upward. Therefore, the separation distance between the tower guy wires below the lowest-phase conductor could be reduced. Conversely, it was found the horizontal distance to the tower structure needed to be increased. As a result of these observations, it was evident detailed insulation coordination would be necessary when using composite material towers on high-voltage transmission lines. To limit overvoltages, the use of surge arresters on overhead lines supported by composite towers is recommended.
The tests on the prototype showed the flashover strength and path could be significantly influenced by relatively small design features. Not only were they vital to qualify and prove the concept, but they also helped to improve the confidence of those responsible for ensuring the design would satisfy the objectives of this project. The tests also confirmed the theoretical calculations and provided valuable input for optimizing the design before the full-scale test. The final composite tower design was electrically qualified by full-scale lightning and switching impulse testing in 2021.
The testing program required to qualify and disqualify composite material samples exposed large differences in seemingly identical products. Nevertheless, the testing methodology was able to identify valid composite materials for use on all voltage levels.
One of the key aspects of this project was the ability to use existing theoretical knowledge to design a tower using composite materials that would satisfy Statnett’s future policy, with respect to 420-kV overhead transmission system lines:
Arild Kvamme Berstad graduated from Bergen University College while working as an electrical engineer in Statnett SF’s transmission line department. As a senior engineer, he is committed to the maintenance of existing transmission lines, ensuring the lights stay on. Berstad is cited as the main author of the CIGRE paper, “Electrical Design and Testing of Composite Towers for 420 kV,” which received a Best Paper Award during the CIGRE 2020 e-session.
Kjell Halsan is the section manager of the electromechanical section in Statnett SF’s transmission line department. He has extensive experience with electromechanical design of transmission lines, having participated in various research projects on the electrical components and design of transmission lines. Halsan is coauthor of many reports on research projects and, for many years, has been active in several working groups in CIGRE, both as a convener and member, and is currently convener of the B2-CAG study group.
Erwin Platenkamp is a senior overhead line consultant and currently leads the overhead lines group at DNV. As a consultant, he participated in the development of the new high-voltage pole WINTRACK in the Netherlands for TenneT BV, a transmission system operator. He has been a consultant and project leader for various overhead line projects around the world. Platenkamp is an active member in CIGRE work groups and co-authored brochure 818, “Transmission Lines with Fiber-Reinforced Polymer (FRP) Composites.”
Christiaan Engelbrecht is a specialist in insulation coordination with more than 25 years of experience. Currently, he is an independent consultant and associate of DNV in the Netherlands and the Electric Power Research Institute in the U.S. Engelbrecht is an active participant within CIGRE and IEC working groups and has authored several journal and conference publications.
Statnett is the transmission system operator (TSO) in Norway, operating the national grid with more than 11,000 km (6830 miles) of power lines and 36,000 towers. Its role is to develop, run and maintain the transmission grid in Norway as well as maintain international connections to Sweden, Denmark, Finland, the Netherlands, Germany and Russia. Statnett also is tasked with coordinating electrical production and consumption, keeping the grid balanced at all times and supporting the electrification of industries to reduce carbon dioxide emissions. The national grid is operated at 50 Hz, mostly at 420 kV and 300 kV, with 132-kV transmission lines in the rural areas of the country.
In 2020, there was record generation of 153.3 TWh, of which 132.9 TWh was used internally with the remainder exported. The Nord-Link 525-kV high-voltage direct-current subsea cable interconnection between Norway and Germany was commissioned in 2020 and the completion of the North Sea Link between Norway and Great Britain in 2021.

Tension Polymer Insulator Statnett is owned by the Ministry of Petroleum and Energy and regulated by the Norwegian Water Resources and Energy Directorate. With its headquarters in Oslo, it employs some 1500 staff located throughout the country.