In underwater pelletizing, numerous variables in the equipment, process and material affect pellet shape, consistency and quality factors such as fines. Defining the “perfect” pellet depends on the conditions of end use, and achieving that ideal requires understanding of the causes of imperfections. #bestpractices
In underwater pelletizing of plastics, defining the “perfect” pellet is not easy. The end use of the pellet defines the key characteristics that make the perfect pellet for the process. Once the perfect pellet is defined, developing and maintaining a process that consistently produces these pellets is critical. Pp Pipe Making Machine
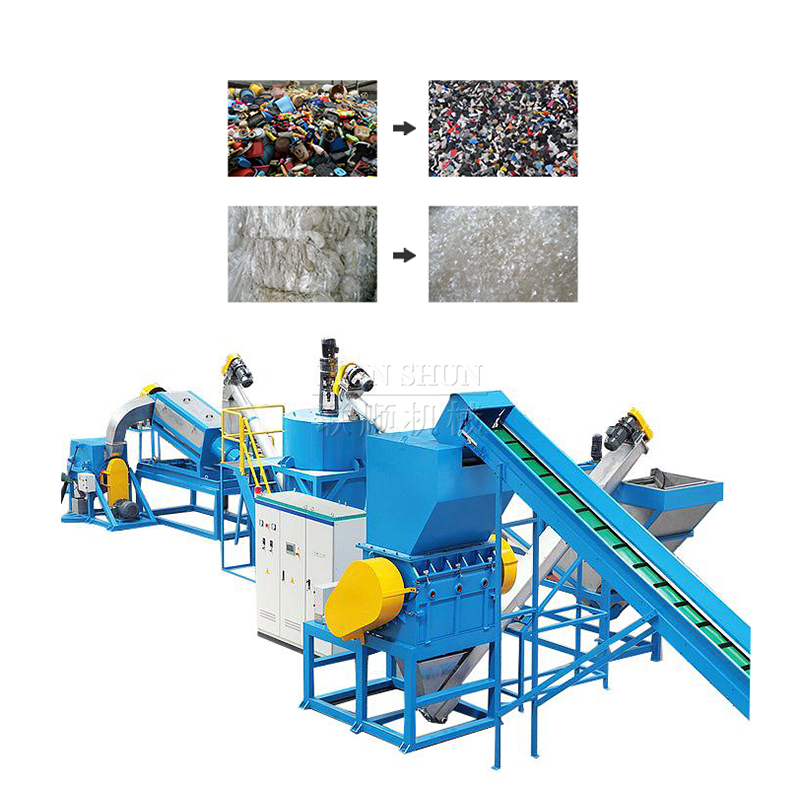
Inconsistent pellet production creates debris, contaminants, oddly shaped pellets and dust/fines — all of which can have a negative impact on downstream processing. Issues like clogging of dryers and resin-handling equipment or variation in how pellets are fed to the screw can be directly related to the quality of resin batch.
Consistency in pellet production is an important factor for compounders, as reliable pellet quality ensures that the end producer has the optimal melt for plastics products, reducing scrap and improving extruded yields, and ultimately improving the customer’s bottom line.
The production line for pellets is a complex system of interconnected pieces of equipment. The underwater pelletizer is a key component but can only be successful with the proper specification of extruders, pumps, filters, water systems and dryers coordinated to achieve consistent pellet quality. Selection of each piece of equipment should be made to achieve an optimum result with the other pieces of equipment.
Even with the best-suited equipment for the job, pellet quality can vary as a result of resin type and additives, melt temperature, die and cutter wear, and process-water changes. The many process variables and their impact on the pellet quality must be understood (Fig. 1).
Additional external influences like human error, equipment adjustments (or lack thereof), and software issues can also have an effect. Having control over these different influences can help create consistent pellets with a predetermined tolerance range, which is a more practical, realistic way to think of a “perfect” pellet.
FIG 1 Variables that affect pellet size, shape and quality. (Photos: MAAG Gala)
While consistency of pellets is the primary metric for measuring perfection, there are some universal standards that we can incorporate to identify a quality pellet:
1. The pellet should be as close to the desired geometric shape as possible.
2. The pellets should be of a consistent size and mass.
3. Each pellet should be clearly separated from other pellets with as little debris as possible (which could break off and create fines).
To understand what a high-quality pellet looks like, we need to understand what pellet imperfections look like, how they are caused, and what producers can do to eliminate or reduce these imperfections and improve consistency.
Tails are created when smearing occurs during the shear-off step.
Compounders are constantly introducing new formulations, including plant-based biomaterials, additives, and colors — producing an unlimited range of materials. This constant evolution creates challenges for pellet producers who need to optimize their processes. Pelletizing system suppliers can be leveraged with their experience and laboratory resources to ensure that a new formulation can be pelletized to the ideal specification and process rates.
Pellet imperfections are often seen as tails, fines, non-uniform pellet size, melt fracture, excessive dimples, voids, irregular shapes, doubles or clusters, chains, agglomerates, wet pellet surfaces, angel hair, and any other negative effects that directly impact the pellet’s polymer or compound properties.
Tails (resembling a comet’s tail) are created when smearing occurs during the shear-off step (Fig. 2). This is often caused by suboptimal temperatures or insufficient process-water flow and pressure, dull cutting surfaces, etc. These tails are often broken off during the drying process, as it spins the pellets around at high speed, whipping off the water and thereby producing the fines. While this drying process improves pellet quality, the fines can collect and clump together within the dryer, requiring increased maintenance and producing scrap.
FIG 2 Microscopic images of pellets with “tails.”
Blade speed (also called tip speed) can have a direct impact on pellet shape and appearance, especially for low-viscosity materials. Figure 3 clearly demonstrate why defining the optimal blade speed is important.
Unwanted particles from compounds and masterbatches may result in high quantities of dust, creating clogged dryer screens and poor pellet quality— and causing significant downtime. Often these inconsistent pellets can be avoided by adjusting speed and operating parameters of pelletizers, adjusting pellet size and cutting temperature. Thanks to advances in technology, modern pelletizers include engineering innovations that allow users to control specific parameters to help reduce fines and improve pellet quality before they arrive in the dryer. Underwater pelletizers combined with innovative dryer technology can significantly reduce, or even eliminate, fines.
Blade speed can have a direct impact on pellet shape and appearance,
The primary challenge in the pellet process is converting molten plastic into useful solid pellets with minimal waste. Creating consistent pellets, with optimal shape, size and consistency suitable for the downstream equipment and applications (whether for molding or re-extruding) is the goal of every production run.
FIG 3 Visual comparison of pellets cut at high and low speeds and with a different number of blades.
The pellets need to be as “perfect” as possible when they leave the dryer, as the finished pellets may be packaged and shipped to remote locations, requiring the pellets to be dry and easy to package, transport, store and unpack. When these pellets are fed into subsequent equipment, they need to be free of contaminants, byproducts or problematic fines to ensure smooth production by the end user.
There are numerous considerations, both upstream and downstream of the pelletizing step, as to what constitutes (and contributes to) “the perfect pellet.” What is clear is that there is no such thing as one-size-fits-all, and that what is most critically important is defining the desired parameters for any particular production run, selecting the partners and suppliers best suited for the job, and ensuring consistency in pellet production to the best of your ability. Consistent pellets are what ultimately will reduce downtime and maintenance requirements, and positively affect your bottom line.
About the Author: Wayne Martin has more than 40 years of experience as an innovator of pelletizing systems. He is technical director at MAAG Gala Inc., overseeing patent portfolio management, and supporting research and marketing. He holds a degree in Mechanical Engineering Technology from The University of North Carolina at Charlotte. Martin began his career as a designer of pelletizing and drying equipment and progressive dies for Gala Industries and went on to management positions in customer service and engineering. He is the inventor or co-inventor of 18 patented equipment and process designs. Contact: 540-884-2589; maagAmericas@maag.com; maag.solutions.
Here's a quick how-to on keeping your pelletizing line churning out quality product.
Plastics made from renewable carbon chains, not fossil carbon from oil or gas, are suddenly a solid commercial reality. The draw isn’t just “green” marketing, but the “green” of stable prices not linked to petrochemicals.
Over the past several years, significant innovations have occurred in the area of polypropylene nucleation.
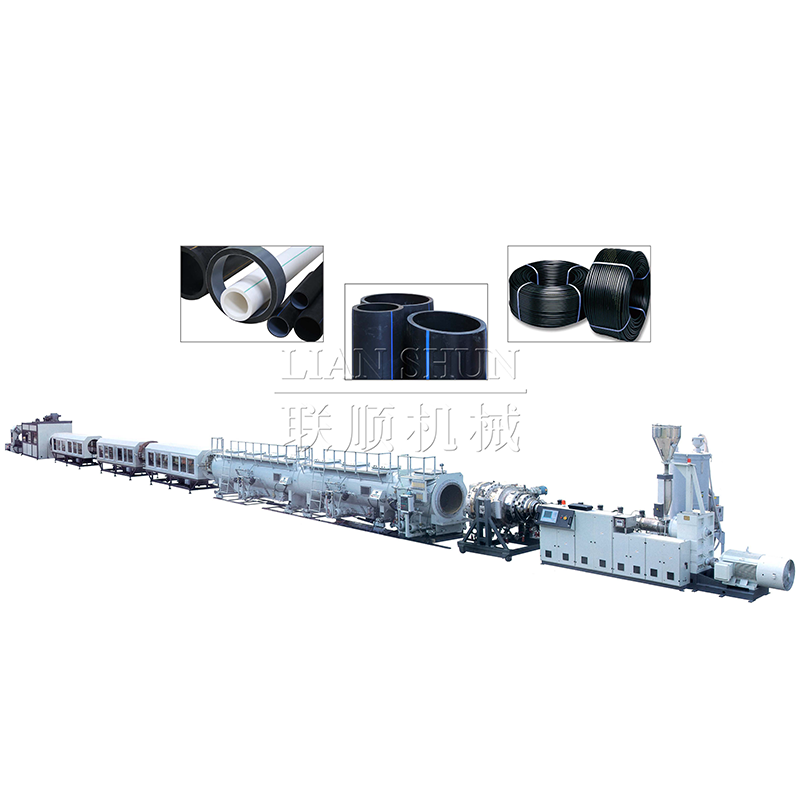
Paper Shredding Machine For Sale © 2023 Gardner Business Media, Inc. Privacy Policy [Log On]