The problem with building automated systems is that it’s hard to look at any problem and not see it in terms of possible automation solutions. Come to think of it, that’s probably less of a bug and more of a feature, but it’s easy to go overboard and automate all the things, which quickly becomes counterproductive in terms of time and money.
If you’re clever, though, a tactical automation solution can increase your process efficiency without breaking the budget. That’s where [Christopher Helmke] seems to have landed with this two-axis add-on fixture for his CNC router. The rig is designed to solve the problem of the manual modification needed to turn off-the-shelf plastic crates into enclosures for his line of modular automation components, aspects of which we’ve featured before. The crates need holes drilled in them and cutouts created in their sides for displays and controls. It’s a job [Christopher] tackled before with a drill and a jigsaw, with predictable results. Cnc Machined Components

To automate the job without going overboard, [Christopher] came up with a tilting turntable that fits under the bed of the CNC router and sticks through a hole in the spoil board. The turntable is a large, 3D printed herringbone gear driven by a stepper and pinion gear. A cheap bearing keeps costs down, while a quartet of planetary gears constrain the otherwise wobbly platform. The turntable also swivels 90 degrees on a herringbone sector gear; together, the setup adds pitch and roll axes to the machine that allow the spindle access to all five sides of the crates.
Was it worth the effort? Judging by the results in the video below, we’d say so, especially given the number of workpieces that [Christopher] has to process. Add in the budget-conscious construction that doesn’t sacrifice precision too much, and this one seems like a real automation win.
*sigh* disappointed it only has more than one axis and not a single axe.
I too was looking forward to seeing an Axe cut the enclosure. Click-bait title!
I’d like to see two axes rotate in 3 axes.
Gotta love the English language – what other language accepts nonsense like “Buffalo buffalo buffalo Buffalo buffalo”, or “Qua qua qua qua qua qua qua” as syntactically valid.
One problem with the buffalo sentence. There are no buffalo in North America. We have bison. Buffalo are in Africa and Asia. https://nationalzoo.si.edu/animals/news/its-bison-not-buffalo-and-other-american-bison-facts
Also, I am far from convinced that “buffalo” is really a verb.
There are several examples of similar constructions on Wikipedia. https://en.wikipedia.org/wiki/List_of_linguistic_example_sentences My previous favourite was the one with 11 consecutive “had” but have to admire the one with 21 consecutive “and”
When flies fly after flies, flies fly after flies.
I think Japansw might win with 子子子子子子子子子子
So in the end, he extended his CNC machine into a full 5 axis design… It would be nice to have some fully open source software for simultaneous 5-axis milling. LinuxCNC can probably handle the motors, but how do you get from a (3D) drawing to CNC vectors? (Please don’t mention that unspeakable autodesk company software *&^%$#@!.
I’m also curious of the use of Vaseline (Petroleum Jelly?) &07:20. Is this a decent lubricant for plastic? I do know that silicone grease works, but it makes a mess of things. Those gears should be shielded from chips to keep them clean (and also keep other things like fingers away), but you can’t have it all in the first iteration.
He doesn’t go into this in the video that I noticed (skimmed through to try and see if he talked about the software), but I’d assume that this is programmed like a 2.5d mill with a toolchanger. It’s likely that he simply generates G-code as per normal workflow, then adds in axis commands to the 2-axis fixture via a script (first program, stitch G91 Z20, G91 Z20 A90, stitch second program, stitch G91 Z20, G91 Z20 A90 B90, etc.) when he stitches the g-codes together. Like you say, full 5-axis control is a complicated thing to integrate, especially when 5-axis can mean any of a dozen different things.
I think G91 isn’t correct, I probably meant G90.
Yes, having a 3D printed cover for the herringbone gear is probably the next step to protect the machine from the ABS dust. It’s not doing simultaneous 5 axis milling. The 2 additional axis are not used while the CNC is working, so it’s perfectly usable with LinuxCNC
So it’s a 3-axis with an adjustable vise.
LinuxCNC can handle simultaneous motion in 9 axes or 9 motors. These are not exactly the same thing, as can be seen in the design being discussed, which has two motors for the B axis. These could be driven identically as a single motor, but it is better to run them as separate “joints” as that allows them to be homed separately. It’s also possible to run a bunch of “extrajoints” which are not part of the coordinated motion planning, but can still be commanded into positions and are part of the homing sequence.
But, yes, full 5-axis machining is very possible with LinuxCNC, and is used by some commercial 5-axis machines.
I played with cnctoolkit some years ago, very dated now but did work.
I’m sure at some point the gears will get cleaned and relubricated. Calm down. Also, no there really isn’t any CAD/CAM software with support for 5th axis routing that isn’t commercial. The hobby CNC scene died with 3D printing’s arrival. Every garage maker flocked to the platform like it’s a holy grail of privaye manufactured goods. Besides, nobody wants to learn feeds and speeds—they want to learn layer-adhesion and flowrates. It’s clean, safe, cheap, produces acceptable results, and won’t piss off the wife the way a chattering endmill on aluminum will at 10pm. That’s why there was never a good open-source 5th axis solution. All the folks “in need and with a can-do attitude” left to develop software for FDM. Not to mention CNC machines, with half the working dimensions, cost 2-3x as much. Add another axis and it’s a suit and tie affair with your bank loan officer. The only other 5-axis cnc for hobbyists that I’ve seen is the NC-CNC, and it’s got a cut area the size of an Idaho potato.
https://forum.freecad.org/viewtopic.php?p=570420#p570420
[Sliptonic], the guy behind FreeCAD’s Path toolbench has got himself a 3+2 setup like the one in the video here, and is apparently working on it. He’s not calling out for help, but my guess is that anyone who has the appropriate machine and wants to help him out with the code would be welcome.
OTOH, as long as your gcode interpreter can run the motors right, it’s easy to cobble the movements in by hand as @fiddlingjunky mentioned.
Oh, also: https://wiki.freecad.org/Path_fourth_axis
I applaud this guy’s efforts, but has he seen this: https://xkcd.com/1205/
That was very satisfying to watch. I love making things, and I also love making things for making things.
In case you were wondering, it’s sponsored by SkillShare. You can skip that bit in the middle now.
i would find it more funny when the box itself was the cnc mashine. like stand the box-cnc next to the to be cnced box. Like these portable magnetic standing Drill mashines. Like a Portable workshop.
Actual portable Workshop could be a nice contest. Like show your tool box or portable 3d printer fixed on a mecerdes repriting instant the lost/broken mecerdes star, or some kind of broken area on a game controller.
so if everyone elso of the readers are ok whit the idea of show your portable workshop contest, than simply reply 1+ under this comment.
Please be kind and respectful to help make the comments section excellent. (Comment Policy)
This site uses Akismet to reduce spam. Learn how your comment data is processed.
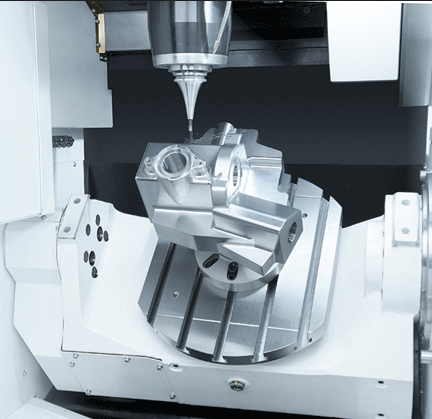
Cnc Aluminum Parts By using our website and services, you expressly agree to the placement of our performance, functionality and advertising cookies. Learn more