Keeping operators from having to manually make sizing adjustments will free them up to do other things for as long as each finishing tool will last, regardless of how many sizing adjustments it requires. #cnctechtalk
All cutting tools start to wear from the very first workpiece they machine. As the tool machines, a small amount of material wears from its cutting tool edge(s). This causes machined surfaces to grow (or shrink) in the direction of the cutting edge(s). Test Strip Cutter
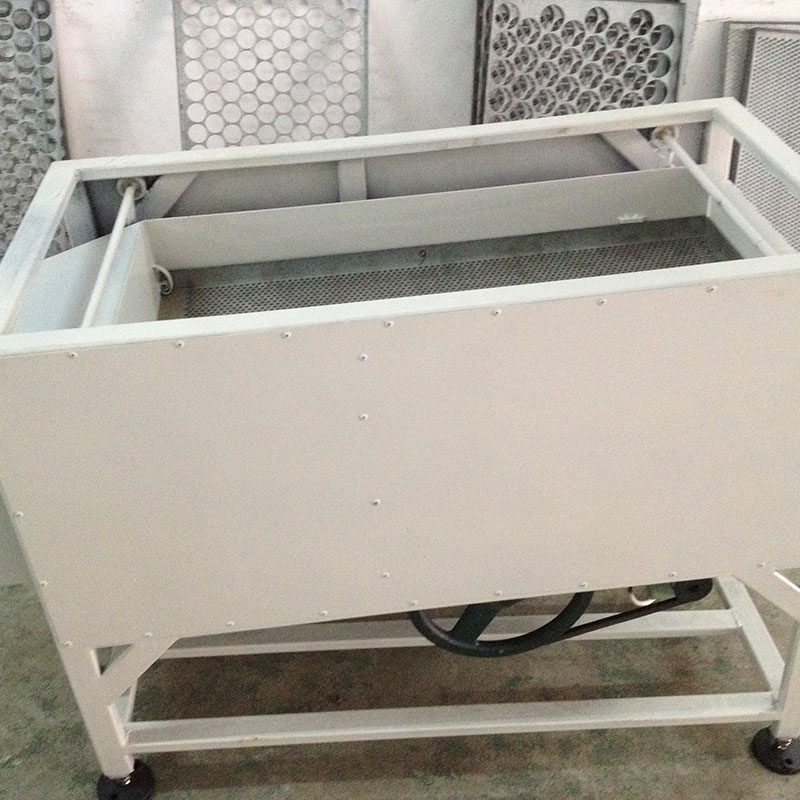
With small tolerances, machined surfaces will grow or shrink to the point that they approach a tolerance limit long before the cutting tool gets dull. When this happens, a sizing adjustment must be made. Indeed, several sizing adjustments may be required during a cutting tool’s life, especially for single-point cutting tools like turning tools and boring bars.
With long running jobs, CNC operators get pretty good at remembering how many workpieces can be machined before a sizing adjustment is required, as well as how many workpieces can be produced before a cutting tool gets dull. While this is the case for any kind of CNC machine, it is especially true with multi-bar-fed turning centers that can run unattended for long periods of time. If not for dull tools and the need for sizing adjustments, the machine could run for many hours — possibly a day or more — without needing an operator present.
While there is not much you can do about the need to replace dull tools, this article will show a way to keep operators from having to manually make sizing adjustments. This will free them up to do other things for as long as each finishing tool will last, regardless of how many sizing adjustments it requires.
This technique requires that you know the same kinds of things mentioned earlier about how cutting tools behave. For example, say you know the new finish turning tool in turret station number 5 can machine 50 workpieces before a diameter sizing adjustment of X-0.0003 inch must be done. And after each additional 50 workpieces, another X-0.0003 inch sizing adjustment is required. And you know the cutting tool can last for 300 workpieces before it must be replaced. Note that many companies provide this kind of information for long-running jobs in production run documentation so operators know how to deal with cutting tools.
Consider this program segment that commands the sizing adjustments to be done automatically:
Look at line N265. It is after the cutting tool’s machining commands and just before the next tool is commanded and calls a custom macro. The arguments (variables) in the command specify how sizing adjustments must be made based upon our proven method.
Arguments T, W, D, A are self-explanatory and values have been set as described in the scenario above.
Argument V specifies the permanent common variable number (#542 in our case) that will be used to count the number of workpiece prior to a sizing adjustment and the number of workpieces prior to the cutting tool gets dull.
A few notes about the application:
Additive manufacturing achieves a large-diameter cutting tool light enough for fast, precise machining of the motor housing’s stator bore.
Correctly specified program zero assignment and coordinate position values enable the CNC to determine how far to move the cutting tool during each positioning motion.

Cnc Rubber Cutting A job shop might have an amount of money tied up in tooling equal to a significant share of its investment in CNC machines. Here is how one shop owner thinks about tool management.