There is much to consider for any industrial hydraulic system. The primary determination is what pump type to use. This is especially important today due to the high cost of power and industry’s demand for energy-efficient systems. In recent years, system designers have sought new ways to reduce energy consumption and carbon footprint. They have also created products that adjust flow and pressure to match the demand of the application.
Hydraulic pumps are the backbone of most hydraulic systems and prime energy consumers. A popular misconception is that pumps create pressure. However, pumps create flow. The pressure in the system is determined by the load on the actuators. Hydraulic horsepower is calculated as a multiplication of flow and pressure and divided by a constant. For a given horsepower, as flow increases, pressure must decrease and vice versa. Electric motor sizes are typically determined by the maximum flow and pressure required for the application; however, maximum flow and pressure rarely occur simultaneously. Therefore, electric motors tend to be oversized, increasing system and energy costs plus unwanted heat losses. Cable Enter Pulley
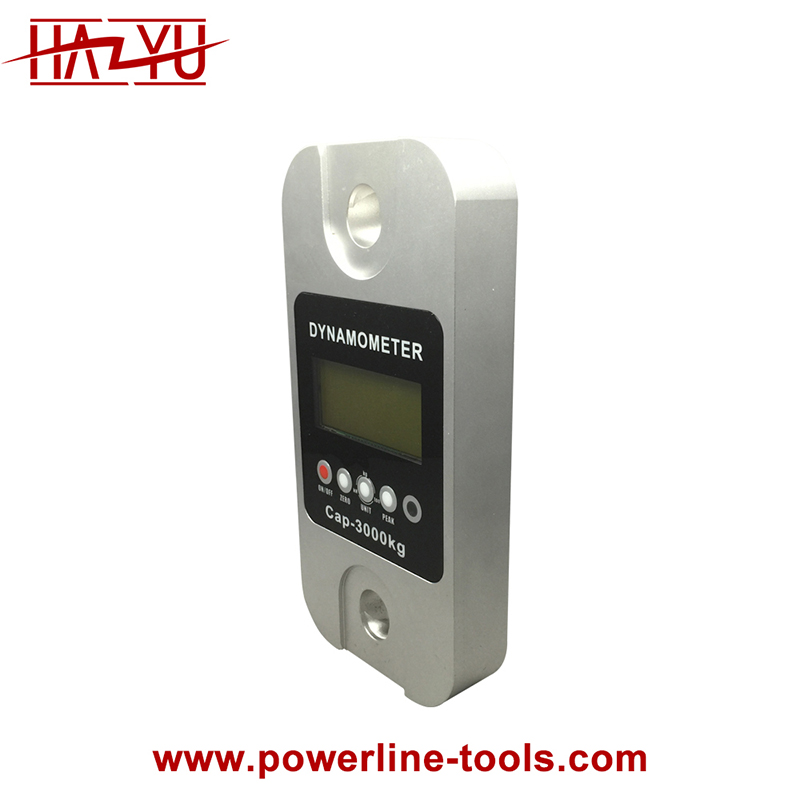
There are a variety of hydraulic pumps, benefits, and issues to consider during the selection process. As the complexity of the pump design increases, so does the initial cost impact.
The most common version of the hydraulic pump is the fixed displacement, which is also the most cost-effective. This pump can be of gear, vane, geroler, or piston design. These pumps are coupled to fixed-speed electric motors, providing constant flow to a hydraulic circuit. The relief valve setting limits the pressure in the system. However, most pumps in these systems are sized for the maximum flow requirement. Any reduction in the flow requirement for a particular machine function means excess flow would bypass the relief valve setting, creating heat and wasting energy.
The variable volume, pressure-compensated pump was a notable change for the hydraulic pump industry. These pumps vary the flow to match the system demand, reducing the heat generated as no flow bypasses the system relief valve. In addition, the pump’s internal pressure compensator determines the system’s maximum pressure. When there is no flow demand on the pump, it reduces output flow to zero but maintains maximum pressure in the system.
Pressure-compensated pumps have decreased wasted energy and improved performance, but the motor selected still tends to be oversized for the application. The development of load-sense variable volume pumps, primarily for the mobile hydraulics industry, improves this situation. Allowing the pump to sense the actual load (or pressure) in a particular function causes the pump to deliver the required flow at load pressure only. This typically requires less energy from the electric motor or engine, reducing operating costs. Mobile equipment engine speed varies with engine control systems, regulated to provide optimum power and torque and minimize fuel consumption. However, industrial applications still use fixed-speed electric motors, and the motor sizing criteria are like standard pressure-compensated pumps.
Recently, hydraulic pump systems have improved with the addition of electronic control with variable frequency drives (VFDs) and utilizing IIoT, leading to transformative reductions in power consumption, noise, and heat loss.
Varying the electric motor speed with a VFD controlling pump flow rates is new, especially with drive costs dropping in recent years. Many power utilities have promoted using VFDs to reduce power consumption and operational costs. While using a VFD in simple applications such as air compressors or fan drives may be adequate, hydraulic system dynamics are much different and require faster response times reacting to machine functions.
Using a VFD with either a fixed or variable pump allows adjustment of input speed to the pump to vary the flow, within the limitations of the pump speed range. However, hydraulic systems move at high frequency, so changing the input speed to adjust flow will not meet the requirements. Another consideration is that squirrel-cage induction motors controlled by VFD only provide constant torque and not constant horsepower. As the speed changes, so does the horsepower to maintain the constant torque requirement (i.e., a 10-hp motor running at half speed is only a 5-hp motor).
Current trends toward connectivity of hydraulic systems via IIoT provide a new opportunity to create energy-efficient pump systems. Using controllers that vary an electric or servo motor speed based on feedback such as pressure and torque allows pump systems to match machine flow and load requirements exactly. If there is no excess flow from the pump system, there is no wasted energy and heat loss.
There are several benefits of a pump system that can match a machine operation’s actual flow and pressure requirements.
Energy Savings. As the pump system monitors pressure, the variable speed induction or servo motor adjusts speed to match the pressure demand. As valves shift and actuators move, pressures in the system change. The control system determines the flow required to match the demand and adjusts the motor speed accordingly. If the machine function is holding pressure for an extended period, the controller will reduce the speed of the motor only to supply the necessary flow to maintain pressure. The constantly changing speed of the motor results in reduced energy costs — in some cases by as much as 80 percent — over traditional fixed-speed pump systems. Additionally, servo motors have a lower inertia and smaller diameter, allowing quicker speed and directional changes.
Reduced CO2 Emissions. Many facilities are looking at their carbon footprint and ways to reduce their impact on the planet. Variable speed demand-based pump systems do just that. When average energy demand declines with a variable speed motor system, so do the offsetting CO2 emissions. As power demand varies and there are minimal power losses during a machine cycle, the associated greenhouse gas emissions can be reduced by up to 70 percent.
Lower Noise. Many manufacturing and assembly facilities establish noise limits for worker safety and comfort. Traditional hydraulic pump systems are noisy and often need to be placed in separate rooms far from the equipment they service. If this is not possible and the pump systems are close to machine operators, noise reduction could be required via costly enclosures. Variable speed demand-based systems tend to be quieter, and the noise quality is more reasonable in close environments to operators. Noise levels well below acceptable are achievable without any expensive enclosures.
Reduced Cooling Requirement. As the demand-based variable speed pump systems match the machine’s flow requirement, far less energy is wasted. Traditional hydraulic systems create heat when the output flow exceeds the requirement of the machine. Hydraulic oil coolers, using either water or air as the cooling medium, are often used to remove 30 percent or more of the installed motor horsepower. These new types of pump systems only need to cool the motor itself, reducing the water flow requirement.
Smaller Footprint. Traditionally, open-loop industrial hydraulic systems require a 3:1 ratio between reservoir size vs pump flow. This rule-of-thumb design consideration allows contamination to settle in the reservoir, additional cooling by increasing the surface area between the oil and the reservoir, and fluid de-aeration. The higher the pump flow, the larger the reservoir. However, in demand-based variable speed pump systems, the design can select a smaller reservoir to meet the average flow demand. A smaller reservoir reduces the cost of fluid required for a particular application and decreases the system’s size by as much as 50 percent.
Simpler Circuit Design. Many machines require proportional or servo valves to vary the speed and provide position control of an actuator. This increases system cost, as proportional or servo valves can be expensive. If tight speed or position control is not required, the variable speed pump system can adjust the flow quickly to suit the variable speed requirement of the actuator. In some cases, proportional valves are replaced with traditional on/off valves at a lower cost and still meet the machine’s functional requirements.
Connectivity. Industry 4.0 or IIoT-compatible devices are now frequently implemented in the machine design phase. IIoT components allow for real-time monitoring and connection to higher-level control systems. Connectivity between demand-based variable speed pump systems and machine control is typically inherent in the software. This connectivity confirms the pump system meets the machine’s demands and provides information for proactive maintenance purposes. Unscheduled hydraulic pump failures are costly and directly impact productivity. However, constant feedback on pump performance will alert maintenance to potential failures and allow scheduled downtime for repair that will not hinder production.
Pump systems have advanced technically over many years. The recent innovations in demand-based variable speed hydraulic pump systems are the next step in lowering energy costs, reducing noise, and allowing for proactive maintenance opportunities.
This article was written by Alan Wheatley, Branch/Shop Manager, Motion (Birmingham, AL). For more information, visit here .
This article first appeared in the December, 2023 issue of Motion Design Magazine.
Read more articles from this issue here.
Read more articles from the archives here.
Watch a Level 4 Autonomous F-150 in Action
3D Printing a Robotic Hand with Bones, Ligaments, and Tendons
How Much Do You Know About Jet Engines?
Scientists Amplify Superconducting Sensor Array Signals Near the Quantum...
5Ws of the Edible Battery
How Much Do You Know About DC Power Supplies?
Understanding Technological Advancements in IR Detection Modules
NVH Prediction in Electric Powertrains: Considering Inverter and Motor Spatial Harmonics
The Path to ISO/SAE 21434 Cybersecurity Compliance
Here's an Idea: Human Factors in Drug Delivery
What Really Changed: A Look at the Updated FDA Guidance Document for ISO 10993-1
10 Tech-Savvy Holiday Gifts for Engineers
Laser Setup Probes Metamaterial Structures with Ultrafast Pulses
Answering Your Questions: Lithium-Air Battery vs. Lithium-Ion
AI Steers Adaptive Control Systems
Comparison Between Wave Soldering and Reflow Soldering
Printed Electronics: The Future Is Flexible
Polycarbonate Seen As Top Choice for LED Lighting
MIT Engineers Design a Robotic Replica of the Heart’s Right Chamber
The Modern Industrial Workhorse: PID Controllers
The Basics of Encoder Selection
AI Helps Robots Manipulate Objects with Their Whole Bodies
Smart Sensor Technology for the IoT
Networking the IoT with IEEE 802.15.4/6LoWPAN
Novel Approach to Advanced Electronics and Data Storage with Ferroelectricity
Laser Beam vs. Electron Beam Welding Which process works best for what?
‘Digital Winglets’ for Real-Time Flight Paths
Mechanical Carbon Materials for Aircraft Seal Applications
Brushless Motors for In-Tank Fuel Pumps
Here's an Idea: A New Minimally Invasive Approach to Spinal Cord Injury
Here's an Idea: Human Factors in Drug Delivery
Here's an Idea: Powerful Sensors for the Eye
By submitting your personal information, you agree that SAE Media Group and carefully selected industry sponsors of this content may contact you and that you have read and agree to the Privacy Policy.
You may reach us at privacy@saemediagroup.com.
You may unsubscribe at any time.

Single Optic Cable Pulley © 2009-2023 SAE Media Group